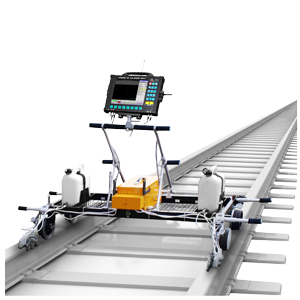
We produce various NDT instruments – from handheld flaw detectors to complex automated inspection systems, which are available worldwide through our network of distributors. Besides the sales, we provide post-sale and warranty services for all our products.
Our equipment utilises a variety of state-of-the-art methods and techniques for non-destructive testing, including ultrasound, phased array, time-of-flight diffraction (ToFD), electromagnetic acoustic (EMA), eddy current, eddy-current array, as well as a wide range of other conventional and custom approaches. We are focused on identifying the appropriate technique or combination of techniques to meet your specific needs.
Our flaw detectors are commonly used in the following industries:
The equipment produced by "OKOndt GROUP" improves the quality of our customers’ finished products and enhances the safety of their infrastructure.
Eddy-current techniques are applied in non-destructive testing of surface and sub-surface layers (detection of metal discontinuities), structure analysis, estimation of coat thickness, dimensions, chemistry, and heat treatment quality. Eddy current testing is based on the analysis of the interaction between external and eddy-current electromagnetic fields that are induced in test objects. Eddy currents are electric current loops which are excited in a conductor while changing the magnetic field that permeates it. The distinctive feature of eddy current inspection is that it can be performed without any contact between a flaw detector and a test object. The interaction is normally achieved at a short distance which is, nevertheless, sufficient for moving the probe relative to the object. This enables the procurement of excellent measurements even when test objects are moving at a high rate of speed.
NDT ultrasonic inspection techniques allow to detect the defects located at a considerable depth in various materials, products, and weld joints. Compared to other non-destructive testing methods, ultrasonic flaw detection has significant advantages: a high sensitivity to the most hazardous defects like cracks or incomplete penetration; high capacity; and the ability to supervise the testing directly from an operator’s workplace with no process interruption – all at low operational cost. Ultrasonic examination is applied in a wide range of industries: energy, heavy machinery, railway, ship building, and the chemical sector. Hundreds of thousands of meters of structural welds, tens of thousands of pipe joints, boiler units, rail weld joints, as well as the quality of pressurised tank parts, forgings, tubes, rolled plates and other products are annually inspected by means of ultrasonic NDT techniques.
The electromagnetic acoustic (EMA) technique is a combined method of non-destructive testing based on three effects of interaction between magnetic fields and the test object: magnetostrictive, magnetic, and electrodynamic effects. The electrodynamic effect is caused by inducing eddy currents in a conductive material that interact with constant magnetic field, which, in its turn, initiates crystal-lattice vibrations (whereas elastic acoustic oscillations occur due to mechanical stresses). EMA transducers are capable of generating horizontally & vertically polarised, longitudinal, shear, Lamb, and Rayleigh waves. Horizontally polarised shear waves have minimum attenuation, diffraction, and metal structure refraction coefficients. The EMA technique allows for non-contact ultrasonic examination of material homogeneity at high temperatures.
June 18-20, 2025
Istanbul, Turkey
Visit the OKOndt Group at Booth No. 2547, Hall 2!
Come and discover our new solutions for ultrasonic and eddy current testing of rails.
15 - 19 September 2025
World Leading Fair for Joining, Cutting, and Coating
Saudi Rail 2024
Riyadh, Saudi Arabia
Airlines for America (A4A 2024)
Nashville, Tennessee, USA
20th WCNDT (2024)
Incheon, South Korea
Railway Intercharge 2023
Indianapolis, USA
The following are the examples of "Boeing" company testing methods implementation with a new EDDYCON C eddy current flaw detector. For regular flights many airlines use "Boeing 737-300, 737-400, 737-500" aircrafts. These aircrafts operational NDT is carried out in accordance with the manual of "Boeing" company (NDT Manual for Boeing 737)
Service life and reliability of railway wheel pairs operation are largely dependent on quality of their components, one of which is the railway axle. Therefore, during manufacture of railway axles it is required to conduct products regular non-destructive testing at all stages of their manufacture for in-time detection of unacceptable defects.
During technical maintenance of BOEING 737 -300, -400, -500 planes (hereinafter referred to as B737) ultrasonic technique of non-destructive testing is widely used (hereinafter referred to as UST).